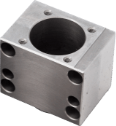
ご相談はコチラ
技術提案
弊社の技術担当者は、検討段階からお見積りの相談、加工時のアドバイスまで、丁寧に提案いたします。
図面を確認し、加工方法や材料についてお伺いした上で、長年蓄積した実績・ノウハウ・技術力を活かして、最適なご提案をさせていただきます。どうぞお気軽にご相談ください。
ラインを構築し
稼働率を向上
同一工程で加工し
加工精度を向上
精度向上のための
形状提案
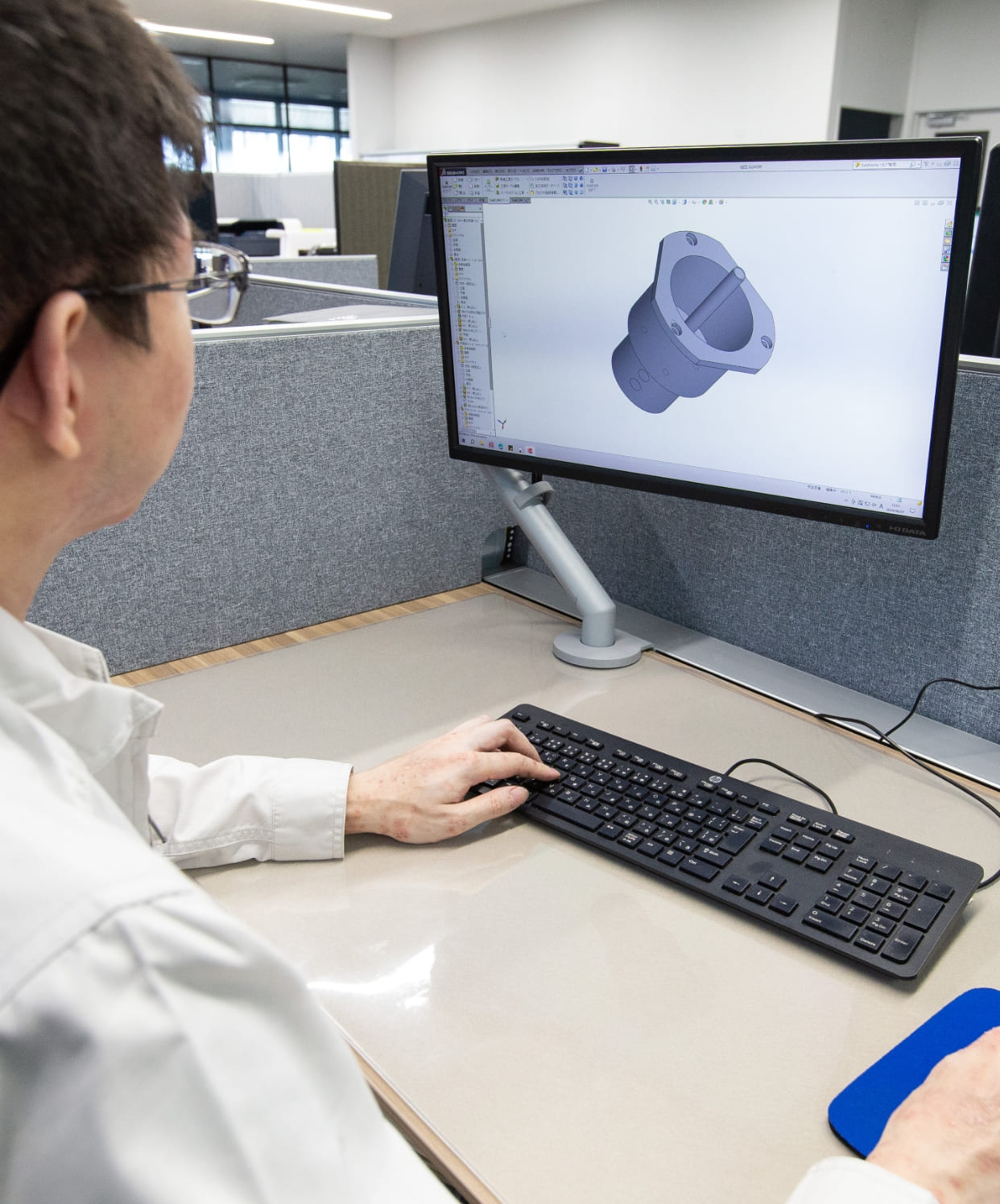
複数の製品を加工できるラインを構築し稼働率を向上
加工工程や製品サイズが異なる3種の製品をそれぞれ
専用ラインで加工していたが、
ライン立上げ当初に想定していた受注数と現在の受注数に差が生じたため、各ラインの稼働率が大幅に低下。
従来のライン構成を見直し、
3種類の製品を単一ラインで加工できる
「複合ライン」を構築。
各製品の異なる加工工程を統合し、
効率的な生産を実現。
【稼働率の大幅な向上】
設備の稼働率が大幅に改善され、従来の25%から大きく上昇しました。これにより、生産効率が格段に向上し、リソースの最適化が実現しました。
【省スペース化】
22台の設備を6台に集約することで、工場内の使用スペースが大幅に削減され、効率的なレイアウトと運用が可能となりました。
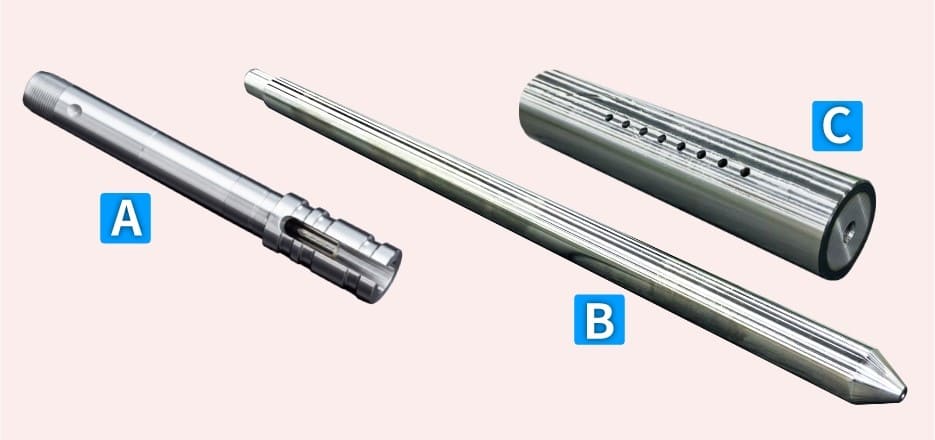
旋削+穴あけを同一工程で加工し加工精度を向上
外径旋削部を基準とする各種寸法が厳しく
(幾何公差0.01、寸法公差±0.01)、
加工精度の安定に苦心していた
基準の外径旋削と穴あけ・フライス加工を同一工程内で行うことが可能な、
最新の5軸マシニングセンタの旋削機能
を活用するアプローチを採用。
これにより、従来の工程間での位置ズレや機械設定の誤差を最小限に抑え、加工精度の飛躍的な向上と安定化を実現しました。この成功事例をもとに、私たちはお客様に対しても、加工精度の向上と安定化を実現する最適なソリューションを提案いたします。複雑な形状や高精度を求められる製品でも、工程集約による効率化と高精度な加工を同時に実現することで、コスト削減と納期短縮が可能です。
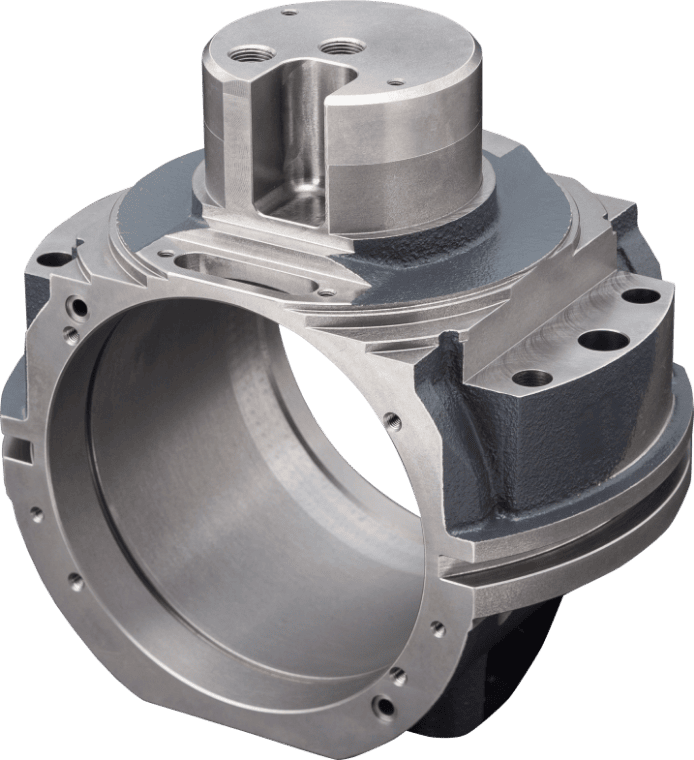
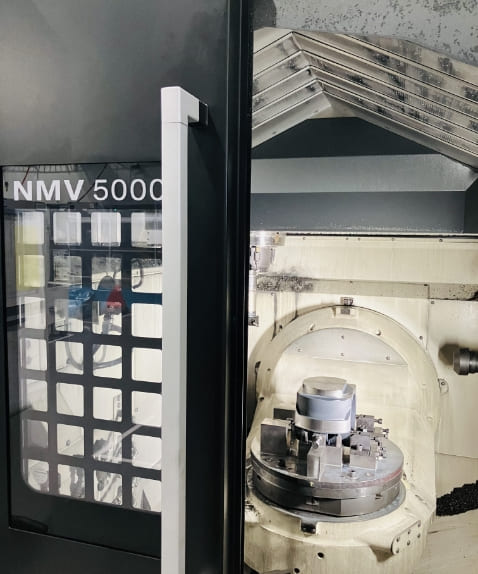
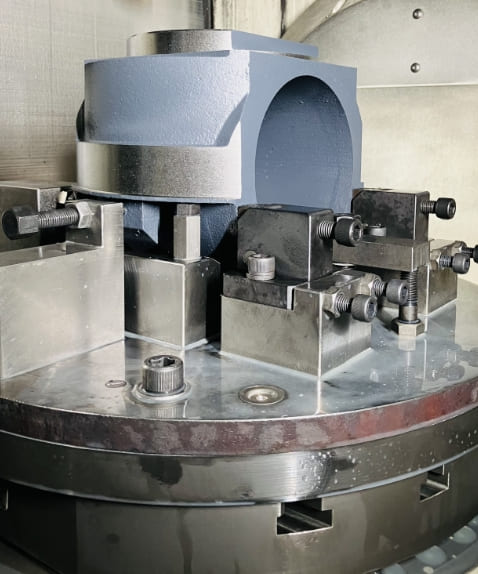
コスト削減・精度向上のための形状提案
- 素材形状により加工時に強力に固定(クランプ)できないため、安定性が欠け、加工に時間がかかる
- 複数の工程で機械加工を行う際、各工程でのワーク取付け直しによる取付誤差が発生し、加工精度に影響
製品の機能や性能に影響を与えない箇所を特定し、その部分に
クランプ座や取付穴の設置を提案。
これにより、ワークの確実な固定が可能となり、加工中の安定性が向上。結果として、加工時間の大幅な短縮が実現しました。さらに、取付誤差のリスクが低減されたことで、複数工程にわたる加工においても精度が安定し、最終的にはコスト削減と加工精度の向上を同時に達成することができました。
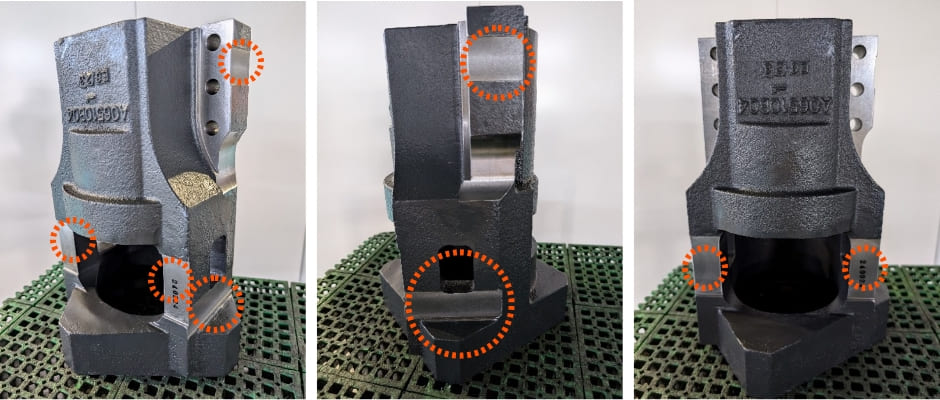
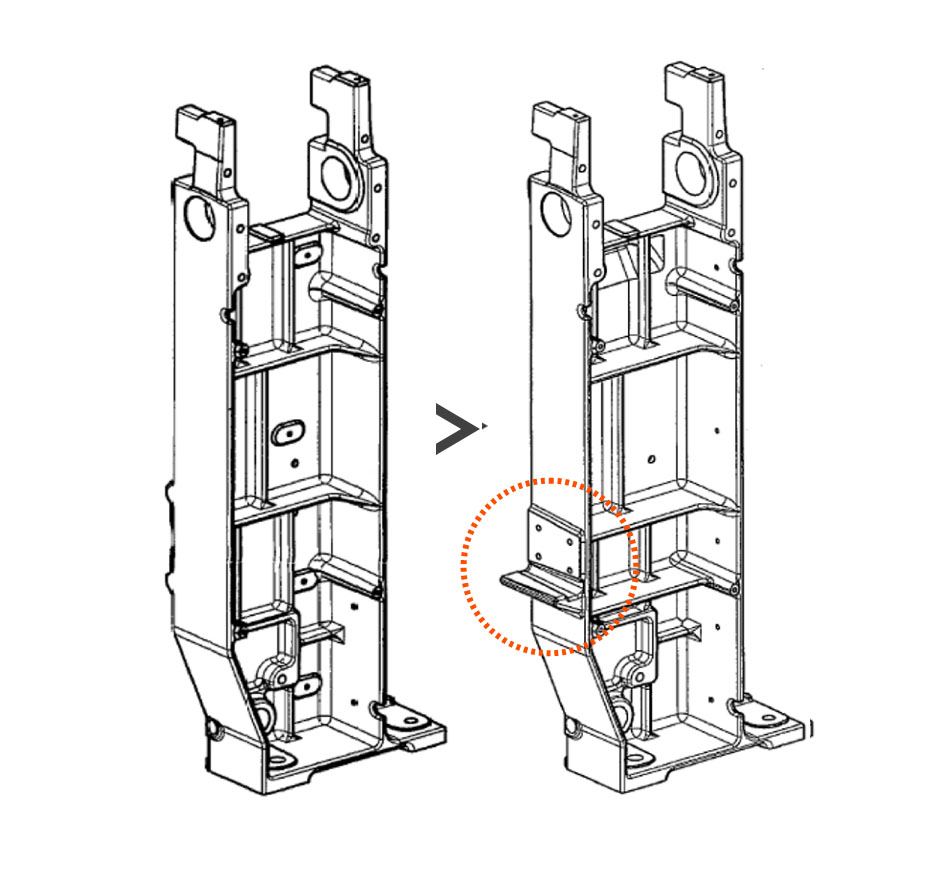
これらの事例は、私たち自身の生産性向上にとどまらず、
お客様に対しても大きなメリットを提供できる提案力へと繋がっています。
多品種少量生産や受注変動に柔軟に対応できる生産体制をベースに、
これまで積み重ねた加工ノウハウとたゆまぬ技術研鑽で、
お客様の多様なニーズにお応えし、お客様の競争力の維持・向上に貢献します。